News
Keeping Vacuum Pumps Cool During Summer Months
Published in: Solar, Press Releases
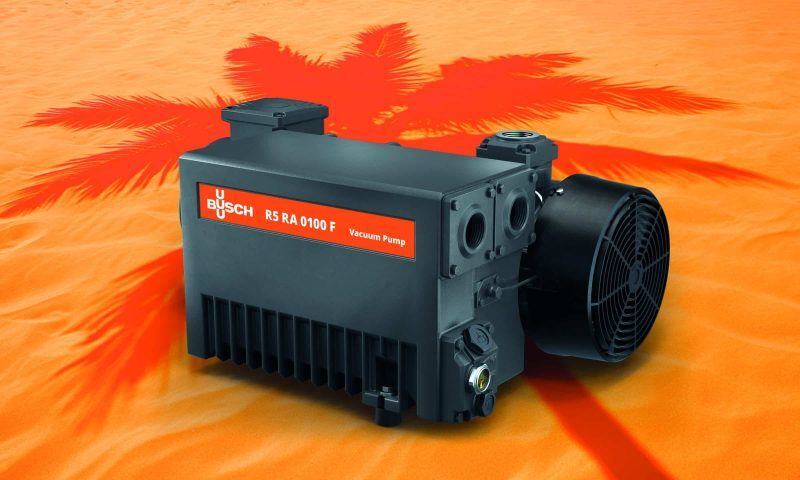
As temperatures rise, the performance and durability of vacuum pumps can be significantly affected. Maintaining a cool environment for these devices is critical, as most are built to function effectively in ambient temperatures of up to 40°C. Overheating can lead to accelerated oil degradation, increased maintenance costs, and potential equipment failure, interrupting manufacturing and causing expensive repairs.
The importance of keeping pumps cool
When vacuum pumps operate in ambient temperatures that are hotter than they are designed for, the oil degrades faster compared to a pump running in a cool environment. This means the vacuum pump oil will need to be changed more often, increasing maintenance costs. If plant room temperatures exceed 40°C, vacuum pumps can overheat, potentially leading to a breakdown. Not only can this disrupt manufacturing processes and lead to lost revenue, but it can also result in costly repairs.
Plant room ventilation – natural vs forced
Natural ventilation from vents and louvres relies on air movement due to wind or convection to be effective, so its performance can vary depending on the temperature and wind speed. During periods of warm weather, it is usually not possible to achieve the high ventilation flow rates necessary with natural ventilation alone, unless significant portions of plant room walls are open or vented.
Effective ventilation for plant rooms
Proper ventilation is essential to avoid overheating in plant rooms. While louvres and vents may offer some relief, they are often insufficient for the task. For confined spaces, implementing forced ventilation systems, such as cooling fans, is crucial to maintain appropriate temperatures. As ambient temperatures rise, the requirement for ventilation also increases, and air in the plant room needs to be changed more often to prevent it from becoming warm.
For example, in an 8m x 4m plant room with equipment heat output of 25kW, the number of air changes per hour needed to prevent exceeding 40°C varies dramatically with the external temperature:
- 26 changes at 10°C outside
- 79 changes at 30°C outside
Estimating the required ventilation flow rate
Typically, 80-90% of the absorbed power of a vacuum pump motor becomes heat exhausted into the room. The following calculation can be used to estimate the required ventilation for an enclosed plant room to keep the temperature below 40°C on a hot summer day. The sum of all the operational vacuum pump motor power ratings can be used to estimate heat emission into the room:
Heat emission (in kW) x 200 = ventilation flow requirement (in m3/h)
Note: Ensure you also consider the ventilation requirements of other equipment located in the plant room.
Heat management solutions
Forced ventilation
Installing a system of fans to exhaust warm air out and draw cool air in is a very effective way of keeping your plant room cool. A control system which can effectively regulate plant room temperature by turning on the required number of fans can enhance energy efficiency.
Exhaust piping
Redirecting the exhaust of vacuum pumps outside the plant room can reduce heat being rejected into the room by up to 35%. Ensure correct material selection for pipework as it can become hot. Also consider insulating the pipe with lagging to protect from hot pipe surfaces and prevent heat from the pipe surface escaping into the plant room.
Heat recovery
Utilizing heat recovery kits, such as those available for certain Busch vacuum pumps, can reclaim up to 80% of the energy used by the vacuum pumps to heat water, providing dual benefits of energy conservation and reduced ventilation needs.
Plant room layout
A well-designed layout can prevent overheating by ensuring adequate space between equipment for proper air circulation. Attention to exhaust and fan directions can also prevent heat transfer to adjacent machinery, which is particularly essential to protect sensitive components such as control systems.
Summary
Keeping vacuum pumps cool during hot weather is key to ensuring their reliability and longevity. Adequate ventilation, heat management solutions, and intelligent plant room design are important strategies. With years of expertise in vacuum technology and systems design, Busch can assist in optimizing your setup for the best thermal management. Reach out to our experienced engineers for your personalized advice and solutions tailored to your unique needs.
About the Busch Group
The Busch Group is one of the world’s largest manufacturers of vacuum pumps, vacuum systems, blowers, compressors and gas abatement systems. Under its umbrella, the group houses two well-known brands: Busch Vacuum Solutions and Pfeiffer Vacuum+Fab Solutions. The gas abatement systems previously offered by centrotherm clean solutions – a former Busch Group brand – are now part of the Pfeiffer portfolio.
The extensive product and service offer includes solutions for vacuum, overpressure and abatement applications in all industries, such as food, semiconductors, analytics, chemicals and plastics. This also includes the design and construction of tailor-made vacuum systems and a worldwide service network.
The Busch Group is a family business that is managed by the Busch family. More than 8,000 employees in 44 countries worldwide work for the group. Busch is headquartered in Maulburg, Baden-Württemberg, in the tri-country region of Germany, France and Switzerland.
The Busch Group manufactures in its 23 own production plants in China, the Czech Republic, France, Germany, India, Romania, South Korea, Switzerland, the United Kingdom, the USA and Vietnam.
The Busch Group has an annual consolidated revenue of close to 2 billion Euro.
Press contact
Dr. Fabian Fahlbusch
Head of Content and Communications
Busch Vacuum Solutions
Schauinslandstrasse 1
79689 Maulburg, Germany
+49 (0)7622 681 – 3379
fabian.fahlbusch@busch.de
www.buschgroup.com