News
More reliable and cost-effective: Schaeffler optimizes wind turbines using closed loop engineering
- Schaeffler is driving the further development of wind turbines through closed loop engineering
- Close cooperation with turbine and gearbox manufacturers to optimize wind turbine efficiency and performance
- Expanded testing capacity for wind turbine bearings thanks to world’s most powerful testing facility in Denmark
Schweinfurt, Germany | July 17, 2024 | Wind turbines have a decisive role to play in the expansion of renewable energy. Schaeffler is a market leader and strategic development partner in the wind technology industry, leveraging closed loop engineering to play a key role that goes far beyond the provision of bearing solutions for on- and offshore wind. Working in close partnership with turbine and gearbox manufacturers, the company supports wind turbine development through state-of-the art system simulation, realistic test-bench testing, and field measurement campaigns.
“This closed loop engineering approach enables us to play a decisive role in further developing wind turbines and making them more cost-effective and efficient,” explains Bernd Endres, Vice President Regional Business Unit Wind at Schaeffler. “As the term ‘closed loop’ suggests, the insights gained through simulation, testing and measurement are fed back into the product development process.”
Schaeffler is presenting its closed loop engineering approach along with various other solutions and services for the wind energy industry under the motto “Driving Wind Energy Together. Innovative. Reliable. Cost-effective.” at the WindEnergy Hamburg trade show from September 24 to 27, 2024 (Hall B5, Booth 333).
System optimization through advanced simulation programs
Optimized bearing design is fundamental to maximizing wind turbine reliability and cost-effectiveness in operation. Hence, Schaeffler’s closed loop engineering approach starts with state-of-the-art calculation and simulation programs. These are specialized multi-body simulation programs that generate highly realistic dynamic models of individual rolling bearings, adjacent structures, and even entire drive trains. The simulations use machine learning and cloud computing to optimize both the mechanics and the dynamics of wind turbine bearings. As well as classic rolling bearings, Schaeffler can run calculations and simulations for the new hydrodynamic plain bearings that it developed for wind turbine gearboxes and that are now in series production.
Powerful test facilities for bearing systems
As the next step in its closed loop approach, Schaeffler subjects its wind turbine bearing systems to comprehensive testing, to ensure reliability. Since as long ago as 2011, it has been using its “Astraios” test bench for large-size bearings to gain important insights into the loads and moments affecting wind turbine drive trains. This facility enables the company to rapidly test and validate newly developed products under realistic conditions.
Schaeffler is currently engaged in a major expansion of its bearing testing capacity. To this end, the world’s most powerful test facility for wind turbine main bearings is currently being built in Lindø, Denmark, in cooperation with LORC (Lindø Offshore Renewables Center) and R&D Test Systems. The facility should be ready to run its first test programs by the end of 2025. Schaeffler played a major part in defining the specifications of the test facility and will use it to test its main shaft bearings in cooperation with turbine OEMs.
Data from field measurements fed back into simulation
The third step in Schaeffler’s closed loop engineering approach, alongside simulation and testing, is field monitoring. This involves Schaeffler experts monitoring prototype turbines in field measurement campaigns. The results of these measurements are then used either to validate the original design parameters from the simulation process or to initiate further optimizations. The focus here is on the drive train, particularly the main shaft bearing system, as this is where all the forces exerted on the turbine add up. These early, design-phase measures enable Schaeffler to minimize system failures and the associated costs while maximizing system robustness.
The closed loop approach also means that Schaeffler undertakes its bearing optimization work in partnership with its customers. In this way, Schaeffler is helping to lower the levelized cost of electricity and drive the expansion of renewable energies.
For more information on Schaeffler’s innovations for wind energy, please click here.
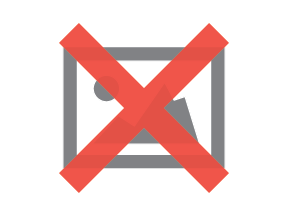
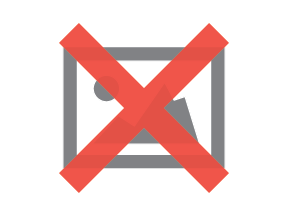
Schaeffler Group – We pioneer motion
The Schaeffler Group has been driving forward groundbreaking inventions and developments in the field of motion technology for over 75 years. With innovative technologies, products, and services for electric mobility, CO₂-efficient drives, chassis solutions, Industry 4.0, digitalization, and renewable energies, the company is a reliable partner for making motion more efficient, intelligent, and sustainable – over the entire life cycle. The motion technology company manufactures high-precision components and systems for drive train and chassis applications as well as rolling and plain bearing solutions for a large number of industrial applications. The Schaeffler Group generated sales of EUR 16.3 billion in 2023. With around 83,400 employees, Schaeffler is one of the world’s largest family-owned companies and one of Germany’s most innovative companies.
Contact
Dr. Thomas Dmoch
Global Head of Marketing & Communications Industrial
Schaeffler Technologies AG & Co. KG, Schweinfurt, Germany
+49 9721 91 3101
thomas.dmoch@schaeffler.com
Johanna Katzenberger
Communications Industrial
Schaeffler Technologies AG & Co. KG, Schweinfurt, Germany
+49 9721 91 5125
johanna.katzenberger@schaeffler.com