News
ABB pioneers drydock-to-drydock turbocharger service concept
Published in: Wind, Press Releases, Renewable News
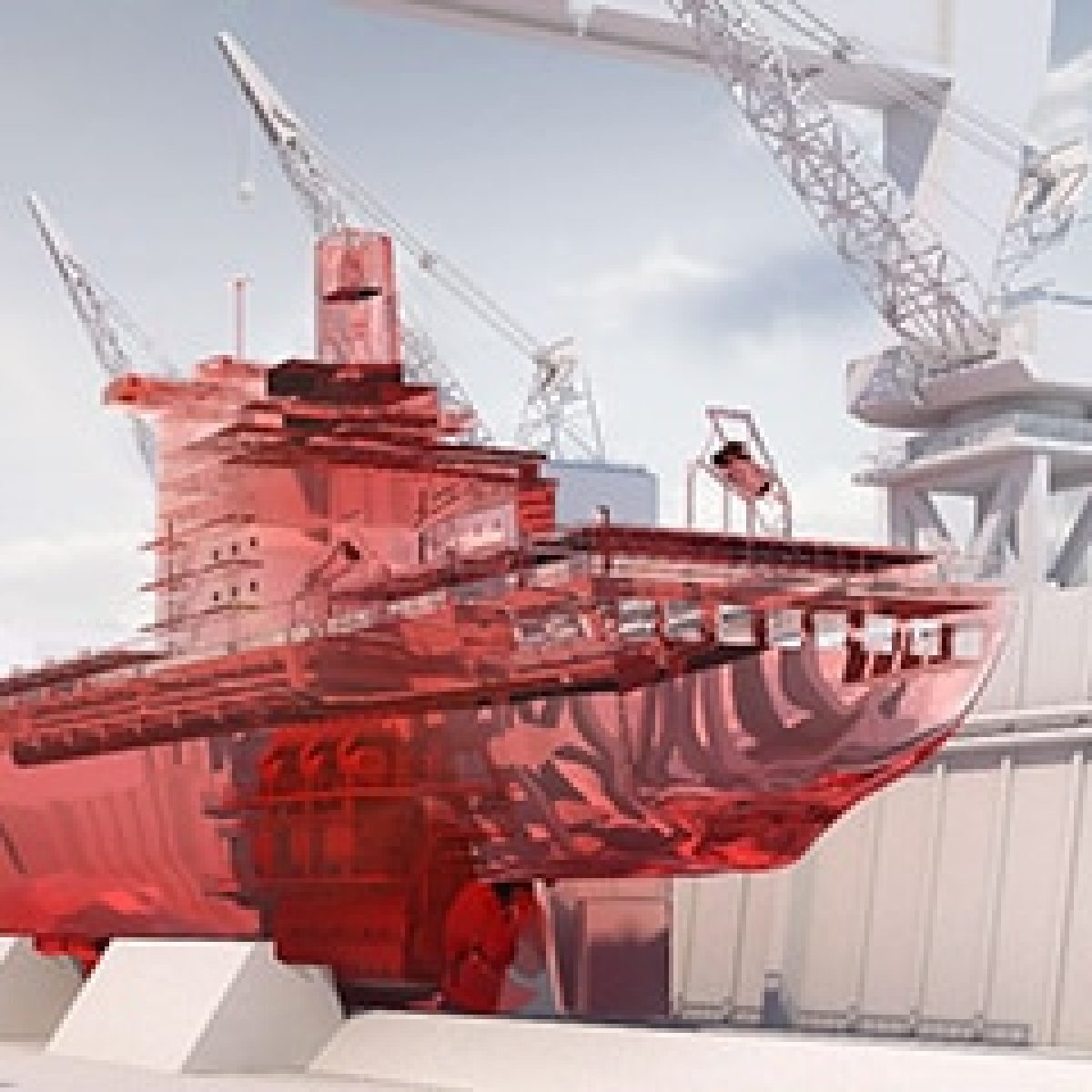
ABB Turbocharging has introduced a holistic service package that offers shipowners financial predictability and peace of mind while reducing complexity and enabling greater insight into equipment health.
Turbo MarineCare offers a turnkey solution to maintenance at a fixed price, providing continuous cover from drydock to drydock. Designed for customers with turbochargers for two-stroke engines, the plan covers standard overhaul parts, wear and tear components, unplanned events (including unexpected repairs), labor, waiting and overtime, and intermediate inspection.
Shipowners are traditionally covered by a limited warranty only in the first few years of a new vessel's life. Turbo MarineCare can be applied from new or at any stage of the vessel or turbocharger's life subject to access to its service history and operating data. By offering comprehensive cover, the service brings the peace of mind afforded by big fleet service agreements within reach of all shipowners.
"In challenging markets, it is even more important for companies to reduce and simplify day-to-day costs," said Roland Schwarz, head of Service at ABB Turbocharging. "Turbo MarineCare allows owners and operators to flatten the cost of turbocharger care over the span of an overhaul period, making their outgoings fully predictable while safeguarding access to original parts, the latest technologies and authorized service teams."
Turbo MarineCare allows operators to dramatically simplify maintenance regimes. Unanticipated replacement of parts and repairs during drydocks can cause delays, administrative burden and extra cost. Under the new service agreement, ABB takes on these risks rather than the shipowner or operator. ABB identifies which parts and service will be required at overhauls and takes responsibility for shipping of parts ahead of drydocking and carrying out the service.
Monitoring of operational turbocharger data is a precondition of Turbo MarineCare. This allows ABB to provide a complete health assessment of rotating components as well as enabling early detection of abnormal data trends that can help to avoid potential turbocharger faults.
"From the moment customers sign up to Turbo MarineCare, the financial risk and worry of the extra cost associated with turbocharger service are removed from themselves and transferred to ABB," comments Roland Schwarz. "This will create peace of mind, eliminate unexpected expenditures and reduce bureaucracy in their daily job."
ABB Turbocharging (www.abb.com/turbocharging) is at the helm of the global industry in the manufacture and maintenance of turbochargers for 500 kW to 80+ MW diesel and gas engines. Our innovative leading-edge technology enables our customers to increase their performance; producing lower emissions and improving fuel consumption even in the toughest environments. Approximately 200,000 ABB turbochargers are in operation across the globe on ships, power stations, gen-sets, diesel locomotives and large, off-highway vehicles. We have over 100 Service Stations in more than 50 countries globally and a wide service portfolio that guarantees Original Parts and Original Service anytime, anywhere.
ABB (ABBN: SIX Swiss Ex) is a leading global engineering company that energizes the transformation of society and industry to achieve a more productive, sustainable future. By connecting software to its electrification, robotics, automation and motion portfolio, ABB pushes the boundaries of technology to drive performance to new levels. With a history of excellence stretching back more than 130 years, ABB's success is driven by 144,000 talented employees in over 100 countries. www.abb.com