Exclusive Articles
Challenges and solutions in factory testing cable segments
Published in: Wind, Talking Point, Exclusive Articles
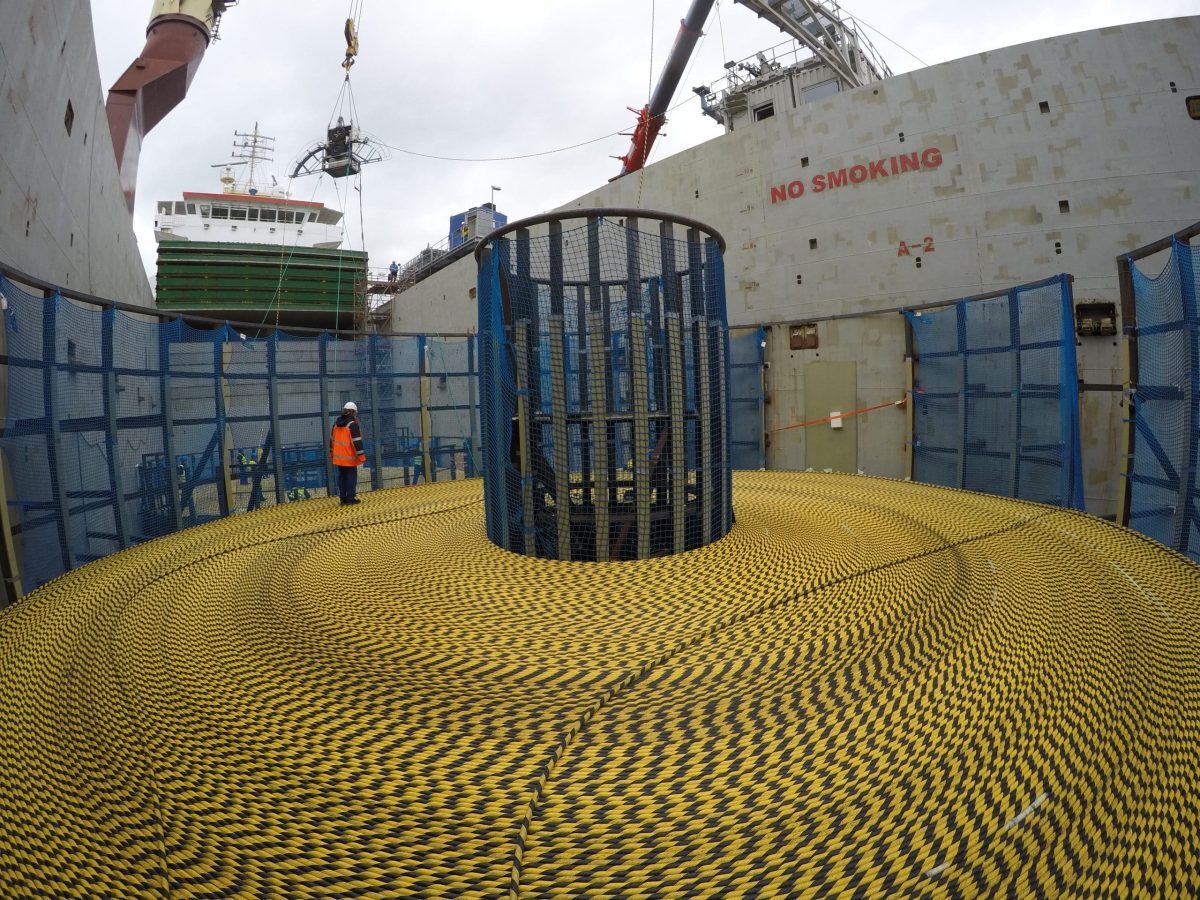
In the current landscape of global energy infrastructure development, the necessity for efficient and reliable transmission systems has become increasingly pronounced, driven predominantly by the imperative of sustainable energy transition. In response to this pressing need, the deployment of high-voltage direct current (HVDC) submarine cables has emerged as a pivotal solution for transmitting electricity over vast distances, particularly across challenging subsea terrains.
The Xlink project stands as a testament to this evolution, aiming to connect Great Britain to Morocco via a sprawling submarine cable network spanning approximately 3800 km. Amidst this ambitious project lies the challenge of ensuring the reliability and integrity of the cable segments, particularly during factory testing. This article deals with the testing of these cable segments, highlighting the challenges encountered and proposing scientific solutions to overcome them.
Resonance principle
At the heart of factory testing lies the resonance principle, a well-established method for generating high test voltages in large-capacity specimens. However, when applied to testing long cables, certain fundamental considerations come into play. The adjustment of inductivity and frequency is crucial in optimising the test circuit for resonance conditions, ensuring efficient testing while minimising losses. Understanding the interplay between resistance, voltage increase, and quality factor is essential for designing an effective test system.
Testing of long cables: technical limitations and solutions
The testing of long cables presents unique challenges, primarily stemming from the escalation of current and losses with increasing cable length. Cubic augmentation of cable losses and the resulting overheating underscores the technical limitations concerning the testable length, particularly at cable ends. Implementing feeding at both cable ends proves instrumental in mitigating losses, significantly reducing them compared to single-sided feeding. Moreover, the optimisation of screen design and material composition offers further avenues for minimising losses and enhancing test efficiency.
To read the full content, please download the PDF below.
Download full article