Exclusive Articles
Bolting in quality and resilience
Published in: Wind, Think Tank, Exclusive Articles
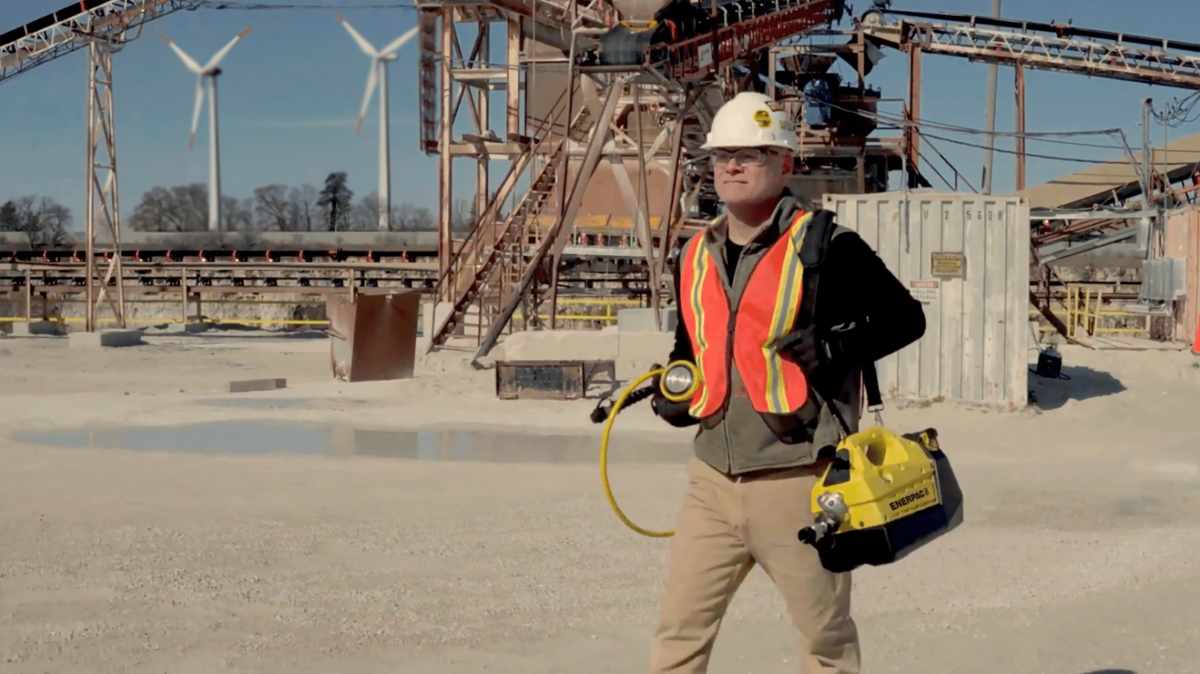
Accurate bolting lies at the heart of the successful installation and maintenance of wind energy structures. Unlike any other working environment, wind energy, both onshore and offshore, represents a major challenge to bolting tool manufacturers. The design of the bolting tool, its resilience and accuracy are going to come under scrutiny as never before.
The need for accurate torquing and tensioning are a given. Now let's add height and accessibility issues, exposure to extreme weather conditions and complexity of turbine structures and components. That's just onshore; go offshore and things get a lot more complicated. Add limited weather windows and the high cost of vessels, now the efficiency of bolting procedures come centre stage, getting it right first time is critical.
Bolting is used to secure the various flanges that make up the wind turbine. These are the base of the tower, the sections that make up the height of the tower, the connection of the nacelle to the tower and finally attaching the blades. It's a lot of bolts.
Depending on the manufacturer, construction of a wind turbine may involve as many as 25,000 bolts. The more powerful and larger the turbine, the more bolts needed. With wind turbines now capable of generating up to 15 MW, bolting is more critical than ever as tower become taller and blades longer.
To read the full content, please download the PDF below.
Download full article